Optimizing inspection technologies for meat carton applications adds another layer of protection for processors as they strive to provide safe, high quality products to their customers. Today’s advanced x-ray machines and software are designed to help processors get the most out of inspection, with a range of built-in tools that keep the line moving while covering more bases. Those looking to invest in new x-ray systems for carton applications can get a real sense of that equipment’s potential performance by identifying variables and conducting multiple tests with their supplier to determine the greatest probability of detection.
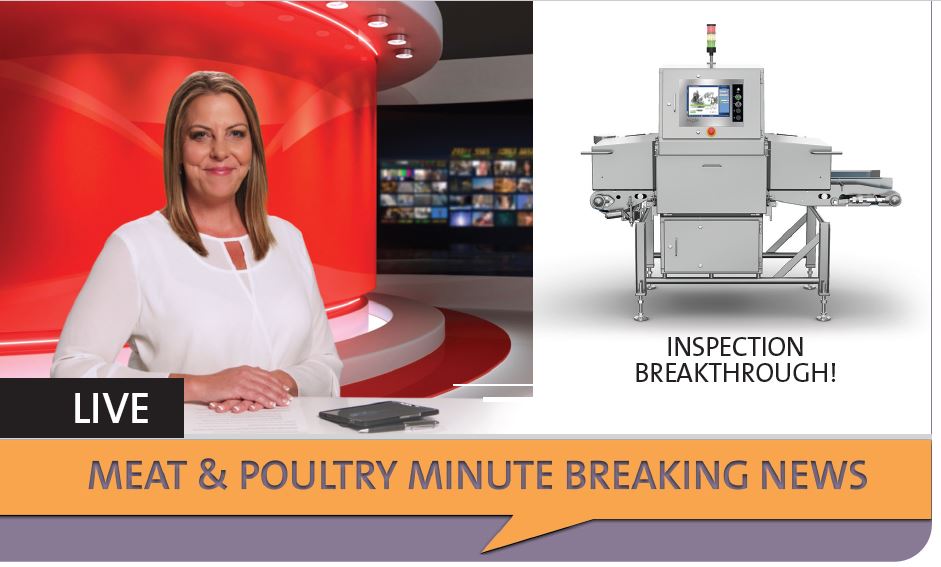
Avoiding recalls at every turn means just that – working to ensure food safety at literally every turn. That includes inspecting cartons of meat as they pass down the line. As part of the comprehensive farm-to-fork effort to protect fresh meat products and to comply with increasingly stringent national and global regulations processors are using advanced inspection systems at more and different points in their facilities to make sure that products are contaminant free. Using x-ray machines for carton applications is effective for a variety of meat products, given the technologies’ ability to discern foreign materials in such “busy” images.
Meat in cartons can be challenging, given the variability of such products on top of an-already tough processing environment, but today’s advanced inspection capabilities can help overcome those potential difficulties. Features within Eagle’s SimulTask™ PRO image analysis software, for example, allow users to filter out certain items in an image to pick up on key information: the software has a special removal tool that can show a clearer image of product, without the crate or carton.
Variability is the proverbial sticky widget in inspecting hard-to-read items and the ability to manage variables is crucial in the inspection process. Managing variables should be an upfront part of the evaluation process when deciding what x-ray system to buy for your line, given the fact that consistent performance is based on understanding possibilities and adjusting to them.
If you’re looking at investing in a new x-ray system for your fresh meat applications, including meat in cartons, you would be well served to determine the probability of detection for your products and processes . Unlike promises of 100% or near 100% detection that just aren’t realistic, a realistic POD defines the likelihood of contaminants being identified and removed based on the product and the many variables involved. By simulating what happens on the line and recreating and testing as many scenarios as possible using the latest inspection technologies, you can get a better sense of how a machine will perform over time and make an informed decision.
More inspection points, more advanced technologies and a realistic perspective for the evolution of performance all work towards shoring up your ability to prevent hazards and costly recalls. With a higher degree of probability comes a higher assurance, for your customers’ peace of mind as well as your own.
To get a clearer picture of your probability of detection, talk to an Eagle expert.